

Archived from the original on October 19, 2006.
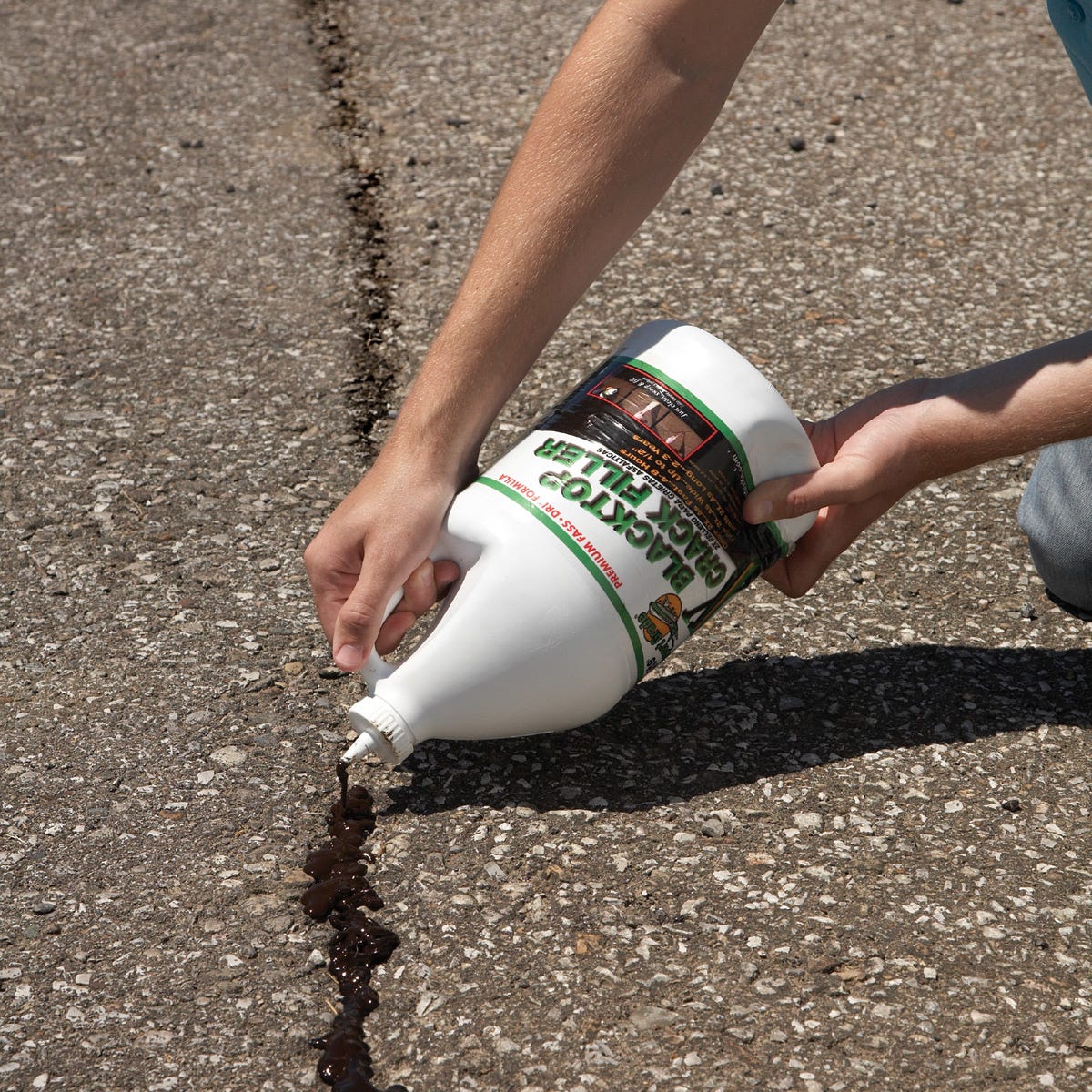
Porous Elastic Road Surfaces (PERS) or poroelastic road surfaces improve RAC by incorporating voids and channels, making the pavement porous and further reducing traffic noise. This means asphalt rubber must be used within 8 hours after production. Two quality control requirements are necessary when using asphalt rubber: (a) crumb rubber tends to separate and settle down in the asphalt cement and therefore asphalt rubber needs to be agitated continuously to keep the rubber particles in suspension and (b) crumb rubber is prone to degradation (devulcanization and depolymerization) and thus lose its elasticity if asphalt rubber is maintained at high temperatures for more than 6–8 hours. In Belgium, tests in the ring of Brussel and in the F1 circuit of Francorchamp (see the film by Jean-Marie Piquint Rubberized Asphalt for Esso Belgium). In 2012, the State of Georgia issued a specification for the use of rubber-modified asphalt as a replacement for polymer-modified asphalt. Tests are currently underway in other parts of the United States to determine the durability of rubberized asphalt in northern climates, including a 1.3 mile stretch of Interstate 405 in Bellevue and Kirkland, Washington and a handful of local roads in the city of Colorado Springs, Colorado. Īrizona has been the leader in using rubberized asphalt, but California, Florida, Texas, and South Carolina are also using asphalt rubber.
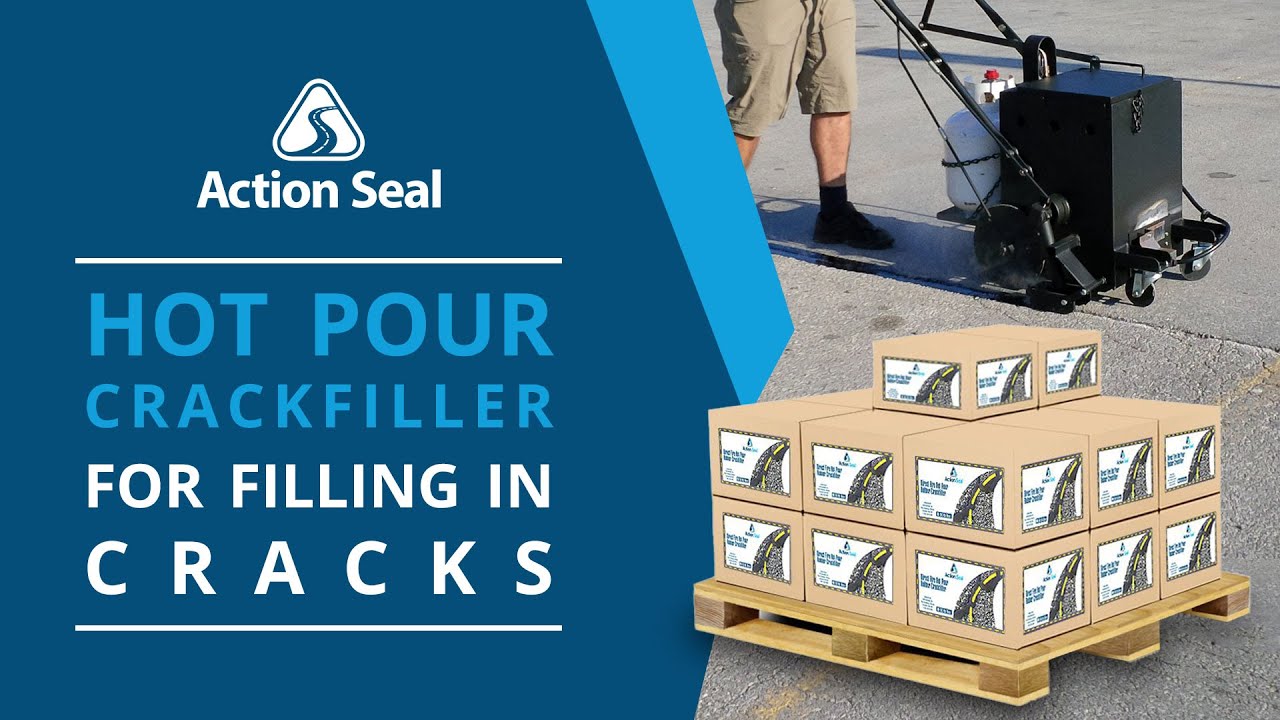
After about one year it was determined that asphalt rubber overlays resulted in up to 12 decibels of in road noise reduction, with a typical reduction of 7 to 9 decibels. In 2003 the Arizona Department of Transportation began a three-year, $34-million Quiet Pavement Pilot Program, in cooperation with the Federal Highway Administration to determine if sound walls can be replaced by rubberized asphalt to reduce noise alongside highways. Since then it has garnered interest for its ability to reduce road noise. Use of rubberized asphalt as a pavement material was pioneered by the city of Phoenix, Arizona in the 1960s because of its high durability. Asphalt rubber is the largest single market for ground rubber in the United States, consuming an estimated 220,000,000 pounds (100,000,000 kg), or approximately 12 million tires annually. This Rubberized Liquid Crack Sealer can be applied with our Crack Banders and our Pour Pots and transferred from the 55 gallon drum to smaller pails for easier handling.Rubberized asphalt concrete ( RAC), also known as asphalt rubber or just rubberized asphalt, is noise reducing pavement material that consists of regular asphalt concrete mixed with crumb rubber made from recycled tires. Do not use in cracks over 1/2" wide.ġ gallon fills 200-225 linear feet of 1/4" x 1/4" cracks. Caution: Do not apply this Asphalt Crackfill below 50 F.
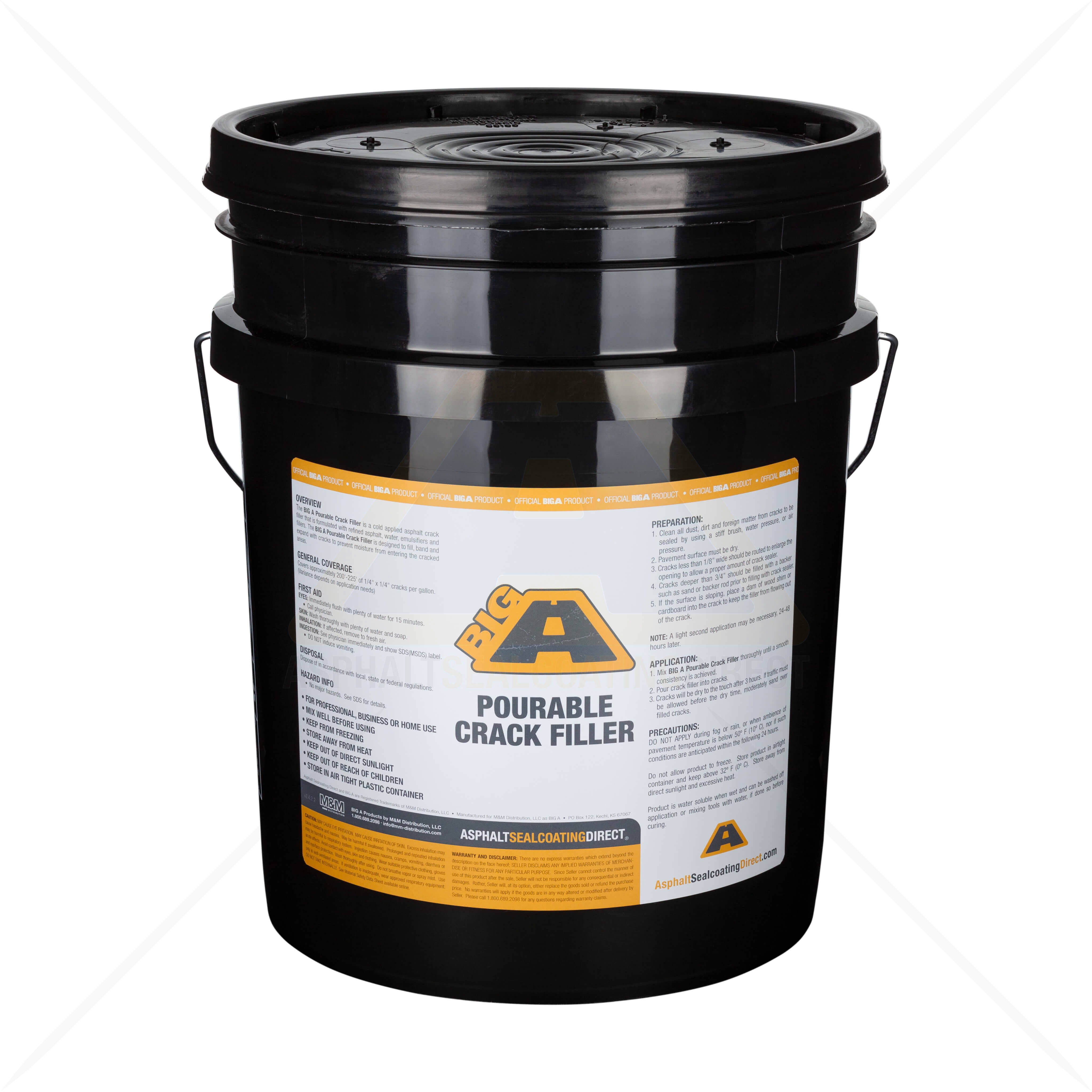
Broadcast dry sand over freshly sealed cracks. Cracks over 1/2" deep should first be partially filled with sand or backer rod. Squeegee off any excess flush with the surface. Apply using a pourpot or mechanical applicator. Made with special blend of latex additives, our cold pour asphalt crackfill is designed to have a higher resistance to re-cracking and last longer than similar alternatives.Ĭlean all loose material from the cracks. It is easily applied using a PourPot and "V" Squeegee and dries quickly usually in less than four hours (we recommend 6 hours to be safe) traffic can be allowed to drive on it and it will not track.
Rubberized asphalt emulsion crack filler professional#
This product is very popular with University's and large projects where they do not want to invest into special crackfilling melters and equipment but have the need to fill pavement cracks with a professional product. Cold Flow Asphalt Crackfill In 55 Gallon Barrels For Large Commercial Crack Filling Applications
